صنعت فولاد
مقدمه
شرکت تیماس رویان اهتمام ویژه ای به صنایع مادر و بالادستی داشته و تلاش فنی و عملیاتی و اجرایی خود را متمرکز بر پیشرفت و توسعه این صنایع به ویژه صنعت کلیدی و استراتژیک فولاد و صنایع وابسته به آن کرده است.
صنعت فولاد به دلیل روابط پسین و پیشین گستردهای که با سایر بخشهای اقتصادی دارد جزء صنایع مادر محسوب میشود. صنعت فولاد بعد از صنایع نفت و گاز دومین صنعت پرحجم تجارت دنیا است. انواع محصولات فولاد به عنوان کالای واسطهای در بیشتر صنایع به صورتهای مختلف کاربرد دارد. مصرفکنندگان صنعتی شامل خودروسازان، صنعت ماشینسازی، صنعت نفت و گاز، صنعت کشتیسازی، صنایع غذایی و مصرفکنندگان ساختمان شامل سدسازی، راهسازی، ساختمانهای مسکونی، تجاری و اداری و هستند. کشور ایران با توجه به برخورداری از معادن غنی سنگآهن به عنوان ماده اولیه مهم در تولید این محصول و همچنین ذخایر عظیم گازی و سرمایه انسانی مجرب در تولید محصولات فولاد مزیت بالقوهای نسبت به سایر کشورها برخوردار است. از همین جهت صنعت فولاد در ایران رشد و پیشرفتی چشمگیر داشته است. ایران در حال حاضر بزرگترین تولیدکننده فولاد در منطقه خاورمیانه و بین 10 کشور اصلی تولیدکننده فولاد در جهان قراردارد.
تاریخچه
اولین تلاشها برای راهاندازی صنعت فولاد در ایران به سالهای قبل از 1930 میلادی برمیگردد. اما بهدلیل وقوع جنگجهانی دوم، پروژهای که قرار بود با همکاری شرکتهای آلمانی راهاندازی بشود، متوقف شد. تقریبا بعد از گذشت دو دهه از جنگ جهانی دوم، با بهبود وضعیت اقتصادی کشور و افزایش تقاضای داخلی برای فولاد، در سال 1338 نخستین کارخانه تولید محصولات فولادی بهنام “شرکت ملی ذوب آهن ایران” پایهگذاری شد. در سال 1351 هم شرکت ملی صنایع فولاد ایران تاسیس شد. بعد از پیروزی انقلاب اسلامی در سال 1358، شرکتهای تولید کننده فولاد در داخل کشور با یکدیگر ادغام شده و شرکت ملی فولاد ایران را با نام اختصاری NISCO تاسیس کردند، NISCO خلاصه شده عبارت (National Iranian Steel Company) است.
ترکیبات فولاد
اگر ترکیبات این فلز را بررسی کنیم، خواهیم دید که ترکیبات اصلی فولاد، آلیاژی از آهن و کربن است. میزان کربن فولاد بین 0.08 تا 1.5 درصد است و این موضوع باعث میشود تا فولاد سختتر از آهن نورد باشد و همانند آهن ریخته شده (چدن) شکننده نباشد. کیفیت فولاد به عوامل مختلفی بستگی دارد. درصد کربن موجود در فولاد، عملیات حرارتی انجام شده و آلیاژهایی که در آن وجود دارد همگی بر کیفیت آن تاثیر میگذارند.
نحوه تولید فولاد
برای تولید فولاد، ابتدا سنگآهن از معادن استخراج شده و در کوره گرم و ذوب میشود و سپس ناخالصیهای آن از بین برده و به آن کربن اضافه میشود. برای تولید فولاد معمولا از دو کوره متفاوت به نامهای کوره ذوبآهن و کوره قوس الکتریکی استفاده میشود. کورههای ذوب آهن عمدتا مواد خام (سنگ آهن، آهک و کک) را با استفاده از برخی فولادهای قراضه برای تولید فولاد استفاده می کنند. در حالی که کوره های قوس الکتریکی عمدتا از ضایعات فولاد استفاده میکنند.
تکمیل زنجیره فولاد
تکمیل زنجیره فولاد دارای مراحل متفاوتی است که بهترتیب عبارتند از:
استخراج سنگآهن از معدن، تبدیل آن به کنستانتره، گندله، آهن اسفنجی، شمش و محصولات فولادی است. برای اینکه بتوانیم با بهرهگیری کامل از این زنجیره به بیشترین میزان ارزشدهی برسیم، باید واحدهایی ایجاد شود که تمامی این زنجیره رویدادها در آن انجام بگیرد. وقتی بتوانیم در یک واحد کل این مراحل را انجام دهیم در این صورت ارزش افزوده ایجاد کردهایم. همانطور که اشاره شد، نخستین و اصلیترین حلقه از زنجیره تولید فولاد، استخراج سنگ آهن است. شرکتها میتوانند با کامل کردن زنجیره فولاد، دست از خام فروشی بردارند و با کامل کردن این زنجیره با اضافه کردن ارزش افزوده آن را با قیمتی بالاتر به کشورها صادر کنند. مخصوصا در زمان حال که میزان صادرات سنگآهن ما به کشورهای دیگه کاهش یافته است. این شرکتها میتوانند خود را توسعه بدهند و اقدام به تاسیس واحدهایی برای رسیدن به مرحله آخر تولید بکنند. البته تاسیس چنین واحدهایی علاوه بر تکنولوژی مورد نیاز به سرمایه زیادی هم احتیاج دارد.
در ادامه با موادی که به ترتیب در زنجیره تکمیل فولاد مصرف و تولید میشوند، آشنا میشویم.
سنگآهن
سنگآهن عنصری فلزی است که از پوسته زمین استخراج میشود. سنگآهن به تنهایی خیلی محکم نیست و به راحتی با اکسیژن ترکیب میشود. برای اینکه این ماده در بخشهایی مثل ساختمانسازی قابل استفاده باشد و استحکام آن افزایش یابد آن را با عناصر مختلفی مثل نیکل ترکیب میکنند، یعنی آلیاژ آن با استفاده از عناصر مختلف تهیه میشود.
کنسانتره
کنسانتره پودری سیاه رنگ است که از سنگ آهن ایجاد میشود. هدف از تولید آن پرعیارسازی سنگ آهن بیکیفیت و کمعیار است. از این محصول برای تولید سایر موارد تشکیل دهنده زنجیره تکمیل فولاد یعنی گندله آهن، آهن اسفنجی، شمش و غیره استفاده میشود. از این محصول در صنایع مختلف مرتبط به ذوبآهن نیز استفاده میشود.
گندله
گُندُله به معنای گلولههای تولید شده از نرمه سنگآهن و سایر مواد افزودنی است. این ماده در ابتدای کار خام است و سپس پخته شده و سخت میشود و در روشهای متعدد احیای مستقیم به کار میرود. گندله ماده اولیه برای تولید آهن خام است و باید در کورههای احیا ویژگی مکانیکی شیمیایی و حرارتی مطلوبی را داشته باشد.
موادی که به ترتیب در زنجیره تکمیل فولاد مصرف و تولید میشوند:
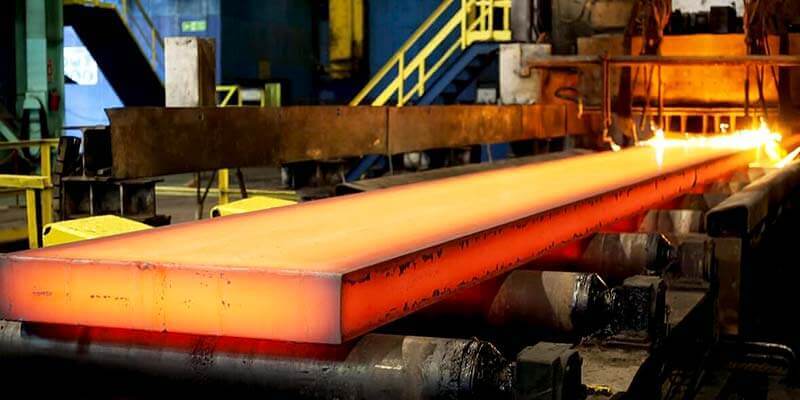
آهن اسفنجی (DRI)
آهن اسفنجی که به آن Direct Reduced Iron هم میگویند، دارای عیار بالای آهن است. محصول حاصل از احیای مستقیم گندله است. در عملیات احیای مستقیم، بدون نیاز به ذوب سنگ آهن، اکسیژن آن حذف میشود. شکل ظاهری آن بهصورت قطعات کروی (گندله) متخلخل یا اسفنجگونه است که دلیل نامگذاری آن هم، همین ظاهر اسفنجی این محصول است.
در ادامه چهار محصول نیمهساخته که بهعنوان فراوردههای میانی نورد فولاد نیز شناخته میشوند را معرفی میکنیم.
شمش (Ingot)
شمشها سطح مقطع ذوزنقهای، مربع و یا دایرهای دارند که طول هر شاخه آن حداکثر ۲ متر است. شکل ظاهری و سایز بزرگ این شمشها حمل و نقل آنها راحت میکند. شمش Steel اولین محصول خروجی از کورههای بلند ذوبآهن است و شکل ظاهری مرسوم آنها همان مکعب مستطیل است. در شکل زیر نمونهای از شمش فولاد را مشاهده میکنید، شکل سایر محصولاتی که نام میبریم نیز به همین صورت است و تنها در ابعاد و سایز متفاوت هستند.
مواردی که در زنجیره تکمیل مصرف و تولید فولاد میشوند:
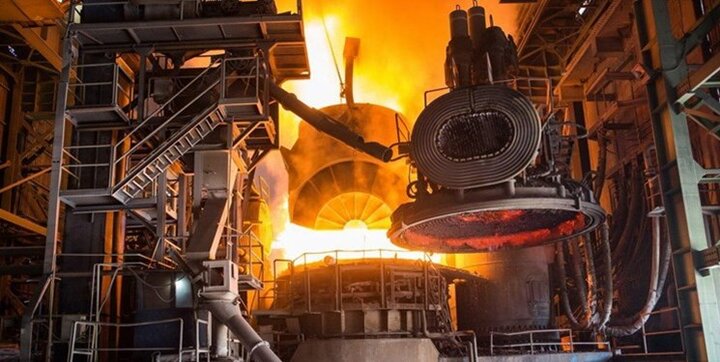
شمشال یا بیلت (Billet)
این محصول طول بیشتری نسبت به شمش دارد. سطح مقطع آن دایرهای یا بهصورت مربع است بهعبارتی سطح مقطعی کوچکتر از 230 سانتیمتر مربع دارد وعرض آن کمتر از 15 سانتیمتر است. از بیلت برای تولید میلگرد، سیم و کلاف استفاده میشود.
شمشه یا بلوم (Bloom)
شکل ظاهری این محصول شبیه بیلت است. اگر عرض بیلت بیشتر از 15 سانتیمتر باشد و یا بهعبارتی دیگر سطح مقطع آن بیش از 230 سانتیمتر مربع باشد، به آن بلوم فولاد میگویند. از بلوم برای ساخت تیرآهن، ریل، قوطی و غیره استفاده میشود.
تختال یا اسلب (Slab)
این محصول یک قطعه فولادی به شکل مکعب مستطیل است که ضخامتی به اندازه 230 میلیمتر دارد. طول اسلب 12 متر و عرض آن برابر با 25/1 متر است. از این محصول برای تولید ورقههای فولادی، تسمه و لولههای جوشی و غیره استفاده میشود. اسلب بهطور مستقیم از اینگت و یا از بلوم ساخته میشود.
تجهیزات و ماشین آلات صنایع فولادی
فرآیند های عمومی و تکنولوژیکی تولید فولاد سبب گردیده ما با طیف وسیع و پیچیده ای از تجهیزات، قطعات و ماشین آلات صنعتی در این صنعت مواجه باشیم. به عنوان نمونه کوره ذوب آهن، سیستم های انتقال و حمل مواد، تجهیزات سنگ شکن فکی یا ژیراتوری، سنگ شکن های مخروطی، صفحات تغذیه کننده، ماشینآلات و تجهیزات سرند، ریختهگری، فورج، نورد و جرثقیل ها از جمله تجهیزات اصلی یک کارخانه تولید فولاد هستند. همچنین وجود انواع نوارنقاله و کانوایرها، انواع انواع بیرینگ ها، غبارگیرها، انواع گیربکس ها، الکتروگیربکس ها، پمپ ها، کمپرسورها، الکتروموتور و غیره وجود تجهیزات ثابت و تجهیزات دوار مکانیکی و الکترومکانیکی را در این صنعت به خوبی نشان کمی دهد. همچنین باید در کنار این تجهیزات به تجهیزات شبكه و پست برق فشار قوی، سیستم های توزیع برق، کنتاکتورها، رله ها و تجهیزات سیستم های اتوماسیون و ابزاردقیق اشاره کرد.
برای نشان دادن تنوع انواع گیربکس صنعتی با کاربری سنگین که در صنعت فولاد به کار میرود می توان به موراد ذیل اشاره کرد:
گیربکس دور متغیر
گیربکس کرانویل یا گیربکس هلیکال صنایع فولاد
گیربکس شافت مسنقیم صنایع فولاد
گیربکس حلزونی
گیربکس شفت مستقیم
گیربکس آویز
گیربکس خورشیدی
اکنون شركت تيماس رويان به عنوان مجموعه ای بهره مند از دانش فنی روز با توان مدیریتی و عملیاتی لازم آمادگی کامل برای تامین و تجهیز، طراحي و ساخت انواع قطعات و ماشین آلات صنعت فولاد و همچنین مدیریت طرح ها و اجرای پروژه های صنعت فولاد از صفر تا صد با بهترین کیفیت و هزینه و در کوتاهترین زمان ممکن را داراست.